Introduction
In the cement industry, the efficiency of raw material unloading directly impacts production line operations and overall costs. As a global leader in cement manufacturing, Conch Cement has consistently pursued smarter, more efficient bulk material handling solutions. In 2023, Conch Cement partnered with NEWTECH to deploy three advanced unloaders for unloading coal, successfully overcoming efficiency bottlenecks and achieving groundbreaking cost-saving results!
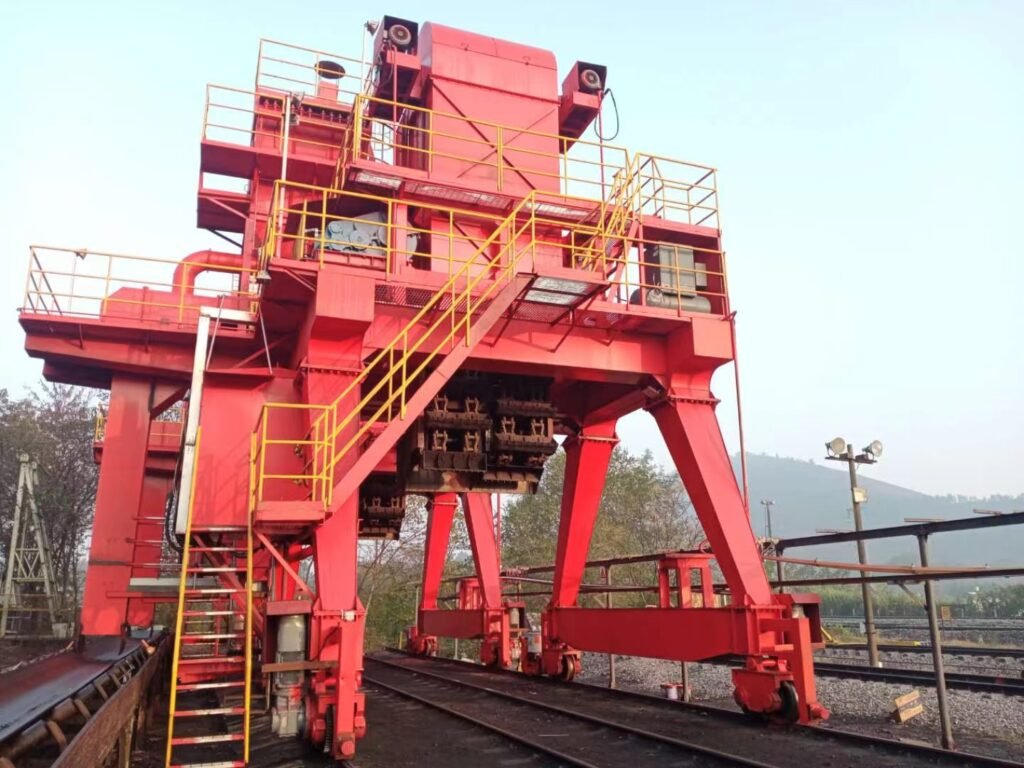
I. Customer Background & Challenges
A large Conch Cement production base faces daily processing demands exceeding 5,000 metric tons of limestone, coal, and other bulk materials. Its original unloading workflow struggled with three critical issues:
- Low Efficiency: Traditional grab cranes required 4 hours per truck, causing severe vehicle congestion during peak periods.
- High Labor Costs: Each shift required 6 workers for coordinated operations, with labor expenses rising annually.
- Environmental Pressures: Open-air unloading led to dust dispersion, failing to meet stringent environmental regulations.
II. Newtech’s Innovative Solution
Tailored to Conch Cement’s needs, Newtech delivered an integrated “Efficiency + Sustainability + Intelligence” solution:
Fully Automated Continuous Operation
The HLM-450 gantry-type chain bucket unloader utilizes a bucket retrieval system and enclosed belt conveyor to enable unmanned, continuous unloading. Single-truck unloading time plummeted to 1.5 hours, eliminating vehicle queuing entirely.
Durability & Energy Efficiency
Featuring high-manganese steel buckets and frequency conversion drive technology, the equipment’s wear resistance improved by 60%, while energy consumption dropped 35%, ideal for high-abrasion materials like limestone and coal.
Zero Dust Emission
A fully enclosed structure paired with intelligent spray dust suppression ensures on-site dust concentration remains below 10 mg/m³, far exceeding national environmental standards.
Remote Smart Monitoring
IoT-enabled modules allow real-time data monitoring from Conch’s central control room. Automatic fault alerts and rapid response guarantee 24/7 uninterrupted production.
III. Results: Data-Driven Success
Since deployment, the Conch Cement base has achieved transformative outcomes:
- Efficiency Leap: Daily unloading capacity surged from 1,200 to 4,000 metric tons, with truck turnover rate increasing 230%.
- Cost Reduction: Labor needs dropped from 6 workers per shift to 1 inspector, saving over 3 million yuan annually.
- Environmental Compliance: Dust-related complaints decreased by 90%, securing provincial “Green Factory” certification.
- Rapid ROI: The investment payback period is projected at 14 months through cost-saving benefits.
IV. Client Testimonial: Why Newtech?
“Newtech’s gantry unloader revolutionized our unloading process. Their technical team not only provided customized designs but also stationed engineers on-site for seamless integration with our existing production line. Raw material supply is no longer a bottleneck—it’s now an industry benchmark!”
— Mr. Zhang, Equipment Department Manager, Conch Cement XX Base
Conclution
With 20 years of expertise in bulk material handling, Newtech delivers energy-efficient solutions for cement, power, and port industries. Trusted by industry leaders like Conch Cement, Jidong Cement, and China Energy Group, we are committed to driving innovation with technology and service excellence.