Goods movement is the pulse of modern trade and economics. The development of a state is dependent on the speed of goods movement in its boundary. Since the dawn of industrialization, wagon goods have been the backbone of the long-distance and bulk goods movement. The process of bulk goods movement may seem easy at first glance; filling, moving, and delivery. But, in the actual case, each of these steps is time-consuming and requires larger manpower. In such a scenario, modernization of bulk material handling is inevitable to shorten the delivery time and to facilitate efficient product control. It’s from this thought the idea of wagon tippler emerged.
Wagon tippler has a long history of bulk material unloading from wagons. They had been an integral part of goods movement through inland and port facilities. The main advantage of using wagon goods movement is the reduced freight rates offered by railroads and reduced manpower requirement.
What is the wagon tipper?

A wagon tippler is an unloading machine that is used to unload bulk material like coal, limestone, ore, etc., from train wagons. A wagon tippler is a part of the tippler system which consists of a wagon tippler, wagon positioning equipment, an underground hooper, and a feeder through which materials are evacuated from the hooper.
They have a rail table mounted on rotary support structures that can lift and tilt wagons to an angle of about 135° which are used at various processing plants such as power, steel, and cement, and for relocating bulk material like core, iron ore, lime.
Usually what a wagon tippler does is that it picks the wagons one by one with its clamping devices. Then the wagons are tippled upside-down to unload all the materials to the hoppers. The materials dumped in the hoppers are fed to industrial plants or ports through feeders. There are several types of wagon tipplers classified based on the type of application, range of weight to be carried, and required processing speed. There are also different types of clamping systems to hold the wagon. The climbing systems can be hydraulic or electrically powered. Before describing different types we must look into the origin and basic construction of wagon tipplers.
Outline
- The origin of the wagon tippler
- Parts of wagon tippler
- How does the wagon tippler work?
- What are the types of wagon tipplers?
- What are the installation conditions of the wagon tippler?
- How to maintain the wagon tippler?
- What should I do if there is still material left after using the wagon tippler?
- The cost is too high and the installation and commissioning period is too long. Is there any other good equipment that can replace it?
- Summary
The origin of the wagon tippler
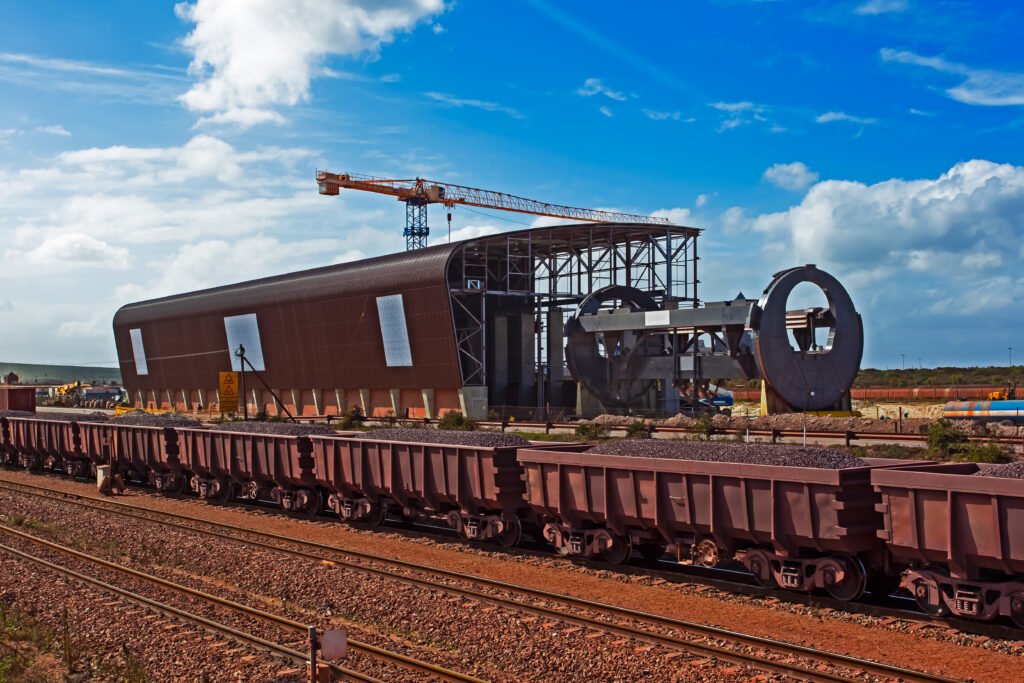
The first industrial revolution rapidly changed the use of technology. The main changes were the use of materials such as iron and steel and the use of fuels like coal, steam power, petroleum, and electricity. Towards the end of the first industrial revolution, the need for coal fuel was at its peak. This led the way to the mechanics of the goods movement of coal and other bulk material transportation.
It was in 1893, the first patent for wagon tippler came into existence. It was Timothy Long who registered the first patent, in this system wagons must be disconnected from the train in order to rotate them. In 1901, Erskine Ramsay introduced the mechanism by which a wagon can unload without disconnecting it from the train. Erskine Ramsay’s idea was to use the train coupling itself as the center of rotation for tippling. Over time wagon tipplers evolved at a fast pace to increase the number of wagons a could dump per minute.
From the 1920s, wagon tipplers were available in different variants. Tipplers started manufacturing for different applications, smaller tipplers were for mine rail applications, and larger ones were used in ports and railroads. Later, various ranges of rotary tipplers and sidearm tipplers were developed that can handle any type and size of wagons.
Parts of wagon tippler
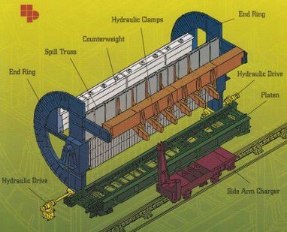
Modern wagon tipplers are constructed following the safety regulations of ISO specification; ISO 3265. Following is the list of the important parts of the wagon tippler system that enables continuous unloading operation:
- Cradle / Platen Assembly
- Circular ring
- Clamping device
- Counterweight
- Wheel grippers and Wheel chocks
- Drive unit
Cradle / Platen Assembly
The cradle is a fabricated steel frame of the table, comprising two main girders, braced together. Between the two layers of the girder, a weighing bridge is placed. When the tippler is in the down position the cradle rests on the two cup & cones and two rollers connecting two stools located on the concrete pedestals or two beams located on the top of the weighing machine. The weighing machine is isolated from any other form of support in order to ensure correct weighing.
The cradle is pivoted and they are positioned off-centered to ensure the tilting tendency that will bring the wagon against the side beam. The cradle on it has an appropriate walkway. To limit the wagon wheels in tipped positions, sections of check rails are given within the rail gauge. A combination of multiple load cells is employed in the weighing system.
End Rings
The end ring is the backbone of the wagon tippler because It holds the entire platform which holds the wagon and rotates when unloading. A tippler consists of a pair of circular ring gear made of strong cast iron. Each ring will be attached to a suitable drive unit.
Two end rings are connected by the spill girder, top clamp beam, and counterweight box girder. To provide the counterweight, half of the end ring is packed with concrete. This counterweight decreases the amount of work needed during the wagon tipping process.
Clamping device
The hydraulic clamping device clamps the wagon with the platform without allowing it to slip. For clamping, dedicated space will be provided in the wagon itself. The clamp is designed to hold the wagon at the predetermined position at the very next movement when the wagon reaches the platform. The clamp holds the wagon until it rests back on the platform. Rubber pads are lined throughout the clamp to reduce the clamping pressure over the wagon walls.
The clamping system is designed so that it can clamp both the maximum and the minimum height of the wagon being tipped. The clamping device will be equipped with hydraulic equipment, an oil tank, and motors and rotate along with the clamping device.
Drive unit and power supply
It is the drive unit that drives the circular ring, thus it is responsible for the rotation of the tippler. The drive unit is either electromechanical or hydraulic. The drive is designed to have coupling, brakes, gearbox, and tooth ring. If the drive is hydraulic, it consists of a hydraulic motor coupled with a helical gearbox and a power pack with an electrical motor.
For both the hydraulic and electromechanical drives, brakes and speed reduction gears are connected to the input shaft of the gearbox. The drive doesn’t allow the tippler to rotate at 360°, but it can tilt the wagon from 135 to 180°. The drive oscillates like a car wiper.
Side beam
The side beam connects the two ends of the circular ring and acts as a support for the wagon while rotating. The side beam made of welded steel moves hydraulic cylinders and touches the wagon standing on the platen. Behind this beam assembly, the spill plates are designed to facilitate the discharge of the contents of the wagons without spillage.
Wheel grippers and Wheel chocks
Wheel grippers are hydraulically operated devices. Two sets of them are fitted to the platform to provide grip for wagon wheels. This will prevent the derailing of the wagon during the tippling operation.
Wheel chocks are also hydraulically operated. They hold the wagon wheel from rolling back or forth from the cradle. They are employed at the inhaul and outhaul side of the cradle.
Sidearm charger
The sidearm charger is the most commonly used wagon positioning device. It is not a component or part of the tippler but is a separate machine. This is a rail-mounted device installed parallel to the wagon line. The Side Arm Charger is a marshaling device to position the loaded wagon centrally on the tippler platform one by one for unloading operation by wagon tippler.
Dust control system
Dust control is an auxiliary system that can be opted for locations where environmental regulations are enforced. While we dump bulk materials from wagons, there is a great chance of dust pollution. A proper dust control system will be recommended by local authorities or railway authorities themselves.
Two types of dust control systems are usually employed in tippling systems; dry and wet dust control systems. Dry control systems require continuous air flow at the correct speed from the correct location and incorrect sizing in order to suppress dust flow. A wet system is designed to provide a moisture cloak over the rising dust cloud. The moisture wets the dust particles causing them to fall back into the hopper.
How does the wagon tippler work?
Now we are familiar with all the important components of a wagon tippler system. All these components work sequentially to achieve the desired task. The step-by-step working of the wagon tippler is described below:
- The loaded wagon is driven to the central position of the cradle system by the sidearm discharger. The wagon is weighed using the weighing machine.
- Once the wagon reaches the rest position in the cradle, the clamp device starts operating. At the start of the rotation, the wagon platform slightly moves upward and tilts. The wagon will safely rest towards the side beam.
- The clamping device gently moves forward to hold the sidewalls of the wagon and locks.
- The wagon reaches a safe unmovable position between the clamp and cradle. The end rings start to rotate. Approximately at a 40° angle of the wagon, the wagon will be safely clamped to the clamping device, and the slow discharge of material will start.
- The rotation continues to the maximum range and the discharge also continues. In this operation, hydraulic power packs are employed to rotate end rings.
- For a couple of seconds, the wagon will be held at the maximum rotating angle to ensure complete discharge of material.
- Then the return cycle starts. The cradle platform with the empty wagon comes to the resting position
- The empty wagon is moved out of the platform to bring the net wagon in. The cycle repeats for the next wagon.
What are the types of wagon tipplers?
For various applications, the size and capacity of wagon tipplers vary. Considering the ease of installation and type of application, wagon tipplers can be chosen between rotary and side-discharge types. Rotary trippers are available in C-type and O-type. Let’s check more about the types of wagon tipplers.
Side discharge wagon tippler
Inside the discharge wagon tippler, the wagon is tilted to a side to fully unload from the top of the wagon. The minimum angle to be titled is 135°, the minimum angle may increase depending on the characteristics of the material.
The end ring in this type of tippler is supported on trunnion bearings. The gear-driven motor runs the end ring gear mounted on its periphery. The movable side beam can move forward/backward, so it should be capable of moving and touching the various widths of the wagon without applying any extra pressure to the sidewall of the wagon. The top clamping facilitates clamping at different heights of the wagon. Which makes the side discharger suitable for unloading wagons at different dimensions. This type of tippler also has the advantage of the low maintenance cost, due to fewer components comparing the rotary type.
There are some disadvantages with the side-discharge tippler. It must lift the wagon while unloading, so the energy demand of side discharge tipplers is much greater. To balance out the mechanical effort, they often need heavy counterweights.
Applications of side discharge wagon tippler:
- Side dischargers are opted usually for when the material is comparatively free-flowing
- It is ok to afford the higher time for 1 tippling cycle
- If the locomotive engine has to pass through the tippler
- Installed where unloading happens in the live railroad.
- Where the depth of the underground hopper is required to be restricted.
Rotary wagon tippler
Rotary tipplers can rotate at a minimum angle of 160° and 180° to completely discharge material. Unlike side discharge tipplers, wagons are supported transversely and held vertically. Then the wagon is rotated to discharge materials. There are two types of rotary wagon tippler constructions; O-type and C-type rotary wagon tippler. Both types are used to provide a faster duty cycle and they don’t require counterweights since they rotate the wagon about their center of gravity.
O-type rotary wagon tippler
O-type tippler is used only in applications where all the wagon designs are the same. All the wagons must be equipped with rotating coupling which allows them to unload without uncoupling. Usually, wagon positioning on the tippler platform is performed using a rope-driven side arm charger.
C-type rotary wagon tippler
C-type rotary wagon tippler is also known as Crescent or C-frame tippler. It is simply an O-type rotary wagon with a section of the end rings omitted which allows the wagon positioner to move straight through the tippler. The wagon is allowed to rotate close to its center of gravity.
Applications of rotary wagon tippler
- Used for non-flowing material
- Applications where customers have larger space to build large hoppers
- The locomotive is not essentially required to pass over tippler
- For faster unloading applications.
What are the installation conditions of the wagon tippler?
The very first thing to consider to installing a wagon tippler is the place where it is going to be installed. The chosen place must be near the railroad and must have enough space to construct underground hoppers. Since the entire construction is underground, the structure must handle possible underground water flow that makes the structure expensive.
The entire wagon tippler system must be at the top of the hopper. The cradle of the tippler should be supported by the concrete beam. All other installation arrangements in the tippler and other auxiliary components must be done as required in accordance with the application. Other common installation requirements are listed below:
General installation conditions for wagon tippler
- The design and installation of tipper components that come into contact with any parts of a car will be so that the equipment or its paints will not be affected.
- The top clamping pressure must be adequate to firmly clamp the wagon at the same time it should not cause any deformation to the wagon walls.
- Each of the clamp tooths that holds the top of the wagon must have sufficient width and rubber pads to provide grip.
- The force exerted between the wagon top and side beams shall not exceed the necessary force to hold the wagon wheel to the cradle throughout the tippling cycle.
- Since the frictional force between the body of the wagon and the side beams can differ, the design of the top supporting beam is not taken into consideration and the load is spread almost evenly over the beam surfaces of the beam.
- The longitudinal beam in the side beam must be as long as the size of the longest wagon. It can be a continuous structure or welded.
- The width of the side supports shall be sufficient to take care of the type of wagons being handled.
- The nature of the material to be unloaded, moisture content, climatic conditions, and other influencing factors should be considered while designing any peripheral appliance.
- Railway specifications must be followed for the designing and construction of rail-mounted wagon tipplers.
Safety requirement for wagon tippler
The wagon tippler system must ensure all the safety requirements recommended by authorities. Here are the general safety requirements for different stages; construction stage, Installation stage, and utilization stage.
Safety requirements for construction
- The design of tippler must avoid the spilling of materials from the wagon
- Automatic devices should be employed to hold the tipplers securely in any position in the event of failure of the drive unit. Also, the system must prevent the wagon from overrunning.
- Proper precautions should be taken to keep the worker’s foot from being trapped between the platform and the tippler’s base.
- Sharp edges and corners must be removed in all workspaces.
- All the regularly used lubrication points shall be accessible without the need to remove the guards.
Safety requirements at the installation stage
- All the tippler specifications must be permanently marked on the tippler. Details such as maximum weight allowed, speed of tippler, and maximum speed at which wagon can pass through tippler.
- Instruction must be stated on the tippler that forbids the operation of the tippler as long as the wagon is not in its tipping position on the platform.
- A mechanism shall be provided to avoid the release of an empty wagon before the tippler is back in its original location.
- A fully integrated control system is recommended for the control of the wagon positioning system, wagon holding devices, and wagon tippler. Controls can be interlocked in such a manner that there is no risk of an accident due to a mistake in the process chain.
- Emergency stop controls are provided in readily accessible locations adjacent to the wagon tippers.
- Both starting and stopping devices should be clearly labeled and made easy to access.
Safety requirements to ensure at working condition
- The inspection, adjustment, maintenance, and cleaning of moving components and of cleaning devices shall be carried out regularly according to the manufacturer’s instructions.
- All clean operations are not allowed when the machine is working. The clean operations can be done before or after the process cycle.
- Qualified operators must be appointed to control the tippler. No other person shall engage in the task.
- Emergency shutdown switches must be installed near the tippler in such a position all the personnel can easily access. The switch must be clearly visible at any condition and it checked periodically.
- In case of an emergency stop, the system is allowed to restart only after determining the cause of the stoppage and repairing the fault.
- To maintain the dust flow, a suitable dust control system shall be installed at a suitable position on the tippler.
How to maintain the wagon tippler?
Wagon tippler is a combination of mechanical and hydraulic machinery. It is natural to cause wear and tear in mechanical bearings. Periodic maintenance is an inevitable process to ensure the continuous processing of tippler. In case of any malfunction, even after maintenance replacement of parts and retesting on programs are recommended.
Here we are gonna talk about maintenance for two sections; mechanical and hydraulic systems.
Mechanical maintenance:
Friction is the main enemy of mechanical failures. The wear of moving parts can be minimized with adequate lubrication. Therefore, for trouble-free activity and long life, periodic lubrication of moving parts/components is very important.
Wear and tear are caused by the excessive use of machines and working in open assembly leads dirt and unwanted particles to enter between the bearing and shaft interface which later on rubs and wears the adjacent part. Considering these facts tippler drive shaft, fluid coupling, overrun, and gear coupling are the main sources of wear and tear.
Driveshaft maintenance
Frequent lubrication of drive shafts must be done with recommended oil and grease. For various parts different oils with different lubricating points are recommended, which is mentioned below:
Part | Lubricating Points |
Line Shaft Bearing | 8 |
Cradle Roller Bearing | 2 |
Cradle Pin Bearing | 2 |
Transfer Beam Hinge | 6 |
Calm Arm Guide Plate | 16 |
To ensure a continuous flow of oil and to ensure that the grease penetrates the bearing, lubrication pipes have to be checked frequently. For the protection of bolts and grease fillings, the gear-style couplings at the output shaft of the gearbox and the line shaft should be tested at every three-month intervals. The teeth of the spur gears at the limit turn drives on the drive unit are regularly greased. Periods of lubrication can be reduced when the atmospheric temperature is high.
Gear coupling maintenance
For every three months, gear coupling should be tested for grease change and security of bolts. After every six months, the connection should be re-lubricated with the recommended grade of lubricant.
Fluid coupling maintenance
The fluid coupling is the connection unit between the motor in the drive unit and the helical reduction unit. It is filled with low viscous oil which is applied at a correct filling angle. Mixing of oil is not allowed because coupling cannot truly happen if oil with different grades is used. 40° is the standard filling angle between a vertical radius and a radius that passes through the filling plug. This might ensure the coupling without slipping unduly and transmit the power efficiently.
Weighing machine
The weighing machine should possess high accuracy at very low maintenance. The cradle should rest on the landing beams on top of the weighted load cells and it should be separated from everything else, particularly around its walkways and at the hinge pins, to ensure correct weighing while the tippler is in down positions.
Overrun
If the overrun of the tippler is detected, it is compulsory to check the tippler system electrically and mechanically including the braking system. The overrun can be due to the wear in the braking system or improper adjustment. So the braking system should be checked first. The mechanical check must also include the security of connections of all components of the switch assembly drive.
It is recommended to test overrun limit switches at every three-month interval. Because, under normal conditions, the limit switches do not operate so after a long period, there is a possibility to develop mechanical and electrical faults.
What should I do if there is still material left after using the wagon tippler?
The wagon tippler is currently the most efficient equipment for handling bulk materials in trains. It only needs to turn over the wagon to unload the bulk materials. However, most of the wagon tipplers have a dumping angle of 165 degrees and are reinforced by steel beams on the inner wall of the wagon. After the dumping is completed, some residual materials will remain in the wagon. Some materials, such as sticky coal, frozen coal, wet sand, and gravel, or materials with a relatively large specific gravity, are more difficult to tip over and clean. Often, a large amount of residual material remains in the train wagons. Currently, manual cleaning is used after the tipping is completed. Workers work hard It has high strength, low work efficiency, and poor working environment. Manual vehicle cleaning requires opening the side door up and down during the tipping process, which poses a great safety risk. On the other hand, manual cleaning of wagons causes dust, which does not meet environmental protection requirements and is also a major hazard to personnel health.
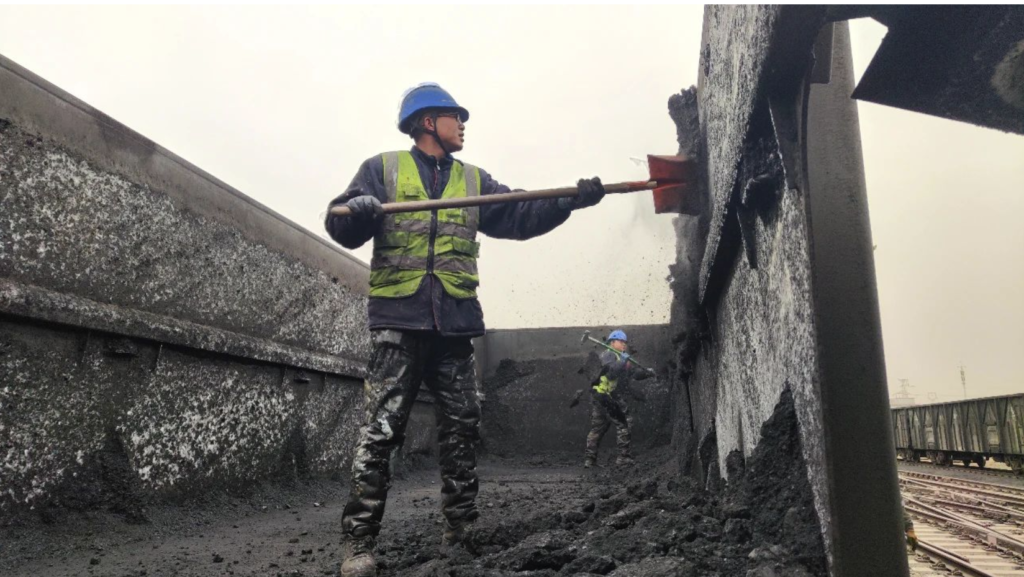
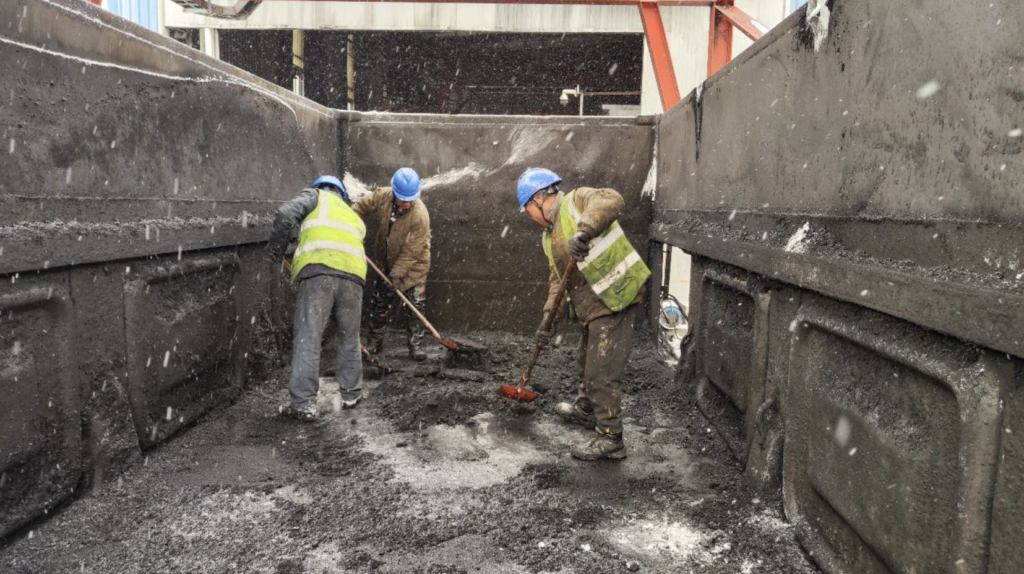
How to solve this problem? At present, NEWTECH, a high-tech company from China, has given a perfect solution. They have designed and developed a wagon cleaning machine that completely replaces manual work. In principle, this equipment can be used as long as there is a train to unload bulk materials (metallurgy, cement plants, thermal power generation, coking, coal preparation, coal chemicals, ports, coal logistics bulk cargo storage bases, etc.). It has the following advantages:
- Safety: There is no need to open the wagon door, and no one is involved in the entire cleaning process;
- High efficiency: it takes 2 to 3 minutes to clean one wagon, and multiple equipment can be operated in conjunction;
- Efficiency increase: One piece of equipment can replace 8 to 10 workers, helping enterprises to mechanize instead of labor and achieve a reduction in staff and increase efficiency;
- Intelligence: One-click start and stop, automatic addressing and positioning, and automatic completion of cleaning operations;
- Environmental protection: The equipment adopts the principle of negative pressure transportation, and the cleaning process will not produce dust.
To learn more, click on the link https://cnnewmachine.com/wagon-cleaner/
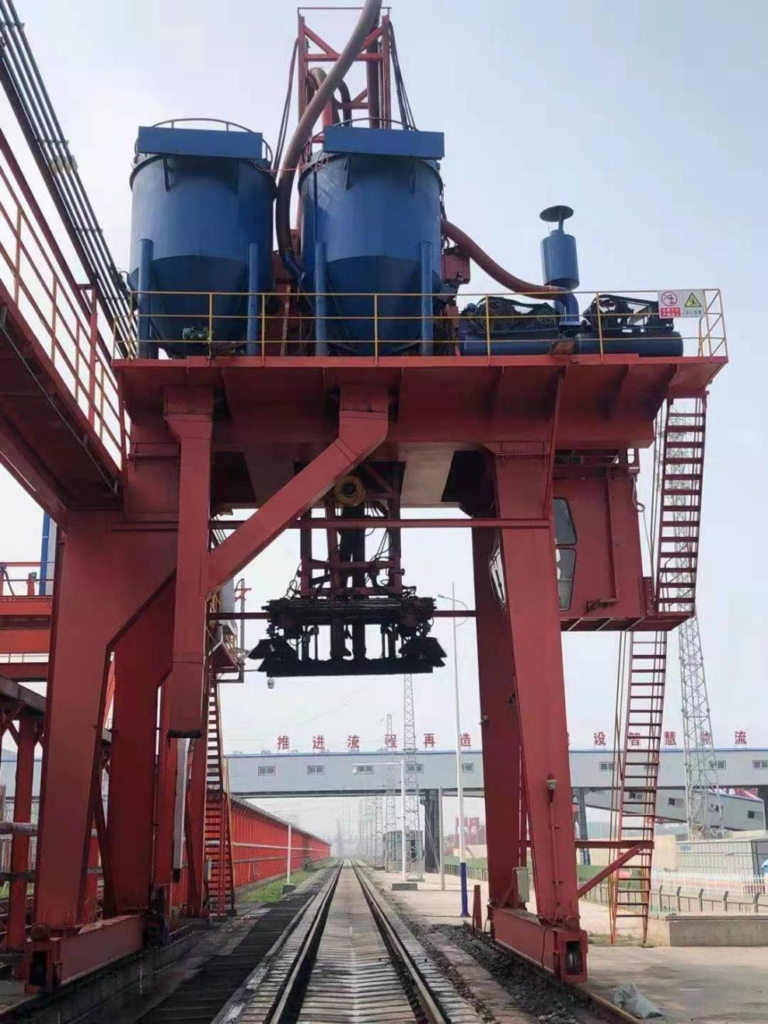
The cost is too high and the installation and commissioning period is too long. Is there any other good equipment that can replace it?
It is important to note that wagon tipplers are suitable for scenarios requiring extremely high unloading efficiency. However, due to their high equipment costs and the need for additional foundation and basement construction beneath railway tracks, the total investment must account not only for the equipment itself but also substantial civil engineering costs, which create significant financial pressure for companies.
To address this, our company has developed a new device – the train wagon unloader – chain bucket unloader. Compared to wagon tipplers, it offers much lower overall costs while maintaining a coal unloading capacity of 600 tons per hour. For sites with sufficient space, some enterprises deploy multiple unloaders to enhance efficiency. The overall performance surpasses that of wagon tipplers, as it requires no foundation construction. Additional civil engineering modifications are minimal—only laying equipment tracks outside the railway lines is necessary.
For aging railway lines needing improved unloading efficiency, train wagon unloaders (chain bucket unloaders) present an excellent solution. Some companies opt to incrementally increase the number of unloaders to progressively boost overall train unloading productivity.
To learn more, click the link: https://cnnewmachine.com/what-is-the-wagon-unloader-chain-bucket-unloader/
Summary
Since the 19th century, Wagon tipplers have been in service for unloading bulk materials and obviously, it will continue for a long period from now. Wagon tipplers are reliable machines for long-term uses. But as we discussed in the article maintenance is an important process just like the installation process of a tippler. A properly installed and well-maintained machine will be an asset for the business.
Looking forward, wagon tipplers are going to be well automated, and more sophisticated control and feedback systems are going to take over the tippler control. Which is going to reduce man-hours.